当社IQCの概要編に続いて、IQC品質管理の重要性と、アリオンのサービスの優れた点をより一層ご理解いただけるよう、本記事では当社の経験からよくあるIQC問題をまとめました。
事例紹介
1. ビデオ機器のコンソール背面カバーには、はっきりとした筋状の跡が見られ、同じ位置に分布しています。
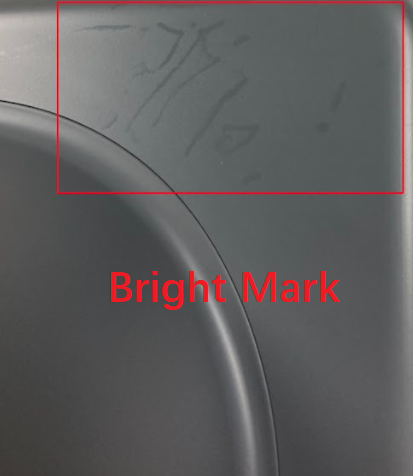
Action Item :
製造元の策定した外観検査基準に基づいて検証したところ、すべてのサンプルに筋状の跡の不良が見つかりました。この問題はかなり深刻なものであり、その程度によって、重大、中程度、軽微の3つに分けられます。評価の結果、中程度の不良を限度見本とし、製造元にはまず選別を行うよう求めました。
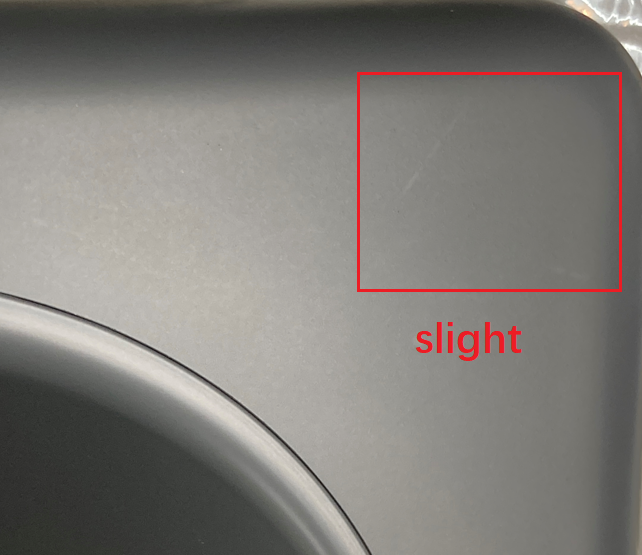
Sampling Rate(サンプリングレート)/Fail Rate(不良率): F/R=996F/1342T=74.22%
Value:
当社は、お客様のニーズに応じて製造元における未検出の不良や輸送に起因する潜在的な不良を特定し、生産開始前にアドバイスすることにより、エンドユーザーのクレーム防止のサポートを行っています。不良状況や生産ラインの生産・出荷のニーズに応じて、製品本来の仕様や検査方法について実践的な提案を行い、短期的な生産・出荷のニーズの解決を図りました。
Root Cause:
製造元に出荷検査記録の確認依頼をしたところ、出荷時にはこのような不良は見られなかったことが分かりました。原因としては高温・高湿で長時間輸送され、包装用のLDPEが化学反応を起こし、帯電防止コーティングがタッチパネル表面に付着したため、タッチパネルの焼付塗装が剥がれて跡が残ったものと推測されます。出荷時期を照合したところ、この問題は製品が長時間高温にさらされたことと密接に関係していると考えられます。
Solution:
主体的に製造元や発注元と打ち合わせを行った後、この問題を改善するため、LDPEを一般的なHDPEに変更することを提案しました。HDPEは耐熱性が高く、筋状の跡の発生を防止できるはずです。新しい包装の投入後、最初の100個のサンプルをすべて検査したところ、不良率は0%となり、このソリューションが有効であることが分かりました。その後、発注元や製造元には、今後の類似機種のQRSの参考として、この検査ポイントを盛り込んでいただくようお願いしました。
2. レンズリングのひっかき傷
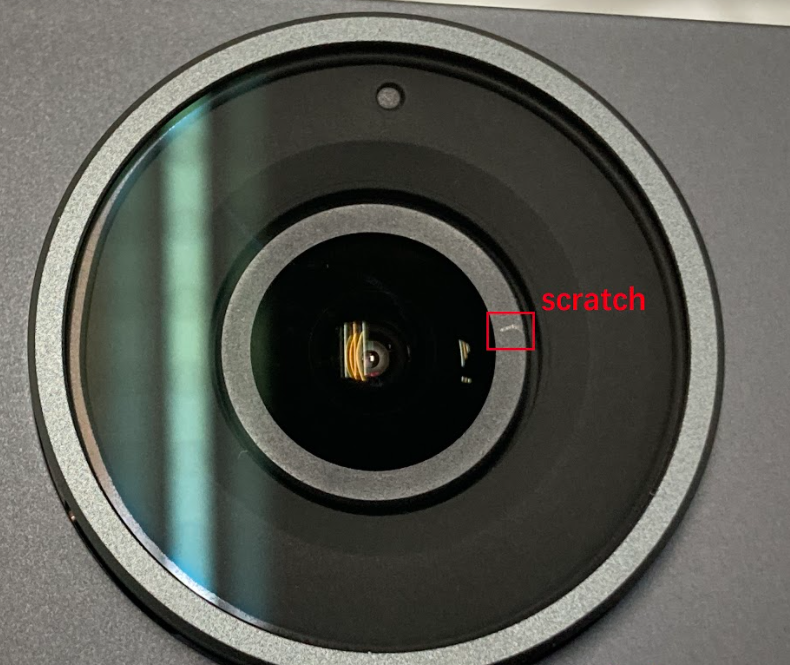
Action Item :
以下のようなひっかき傷の不良が確認されました。どちらも現在製造元が策定する外観基準に適合していません。
Scratch# 1 S=0.3~0.4mm²
Scratch# 2 S=0.15~0.2mm²
追加で20個をサンプリングした結果、同様のScratch# 3 S=0.25~0.3mm²のひっかき傷不良1個が発見され、やはり基準の要件を超えていました。初期判定の結果、この不良は製品の機能には影響せず、実際の操作においても製品のイメージングには影響を与えないと判断されましたが、やはり製造元にFA解析を依頼し、リワークを行うか、外観についての既存の合格水準の変更を発注元と協議してもらうことが必要です。
Value:
外観検査基準に沿って、製造元が把握していない不良や仕様の不備を発見することで、事前に検討を行い、既存の基準を更新することでお客様の出荷要求に対応し、不良箇所が製品の動作に与える実際の影響を検出できるようにお客様をサポートします。
Solution:
組立業者は、このひっかき傷はレンズ製造元の合格品質水準内であり、原材料の製造元が当該の外観上の欠陥はイメージング品質に影響を与えないことを保証している回答しました。当社は、テストチャートで5個をサンプリングしシャープネスとイメージングを確認し、この外観上の欠陥は確かに画像に影響を与えないことが分かりました。また、製造元からは、合格品質水準を上げると、輸送や検査のコストが大幅に上がり、製品の競争力にマイナスになるとの指摘もありました。このため、発注元のお客様と話し合い、この原材料の合格品質水準を完成品検査の合格品質水準に盛り込み、リワークを要求しないこととしました。
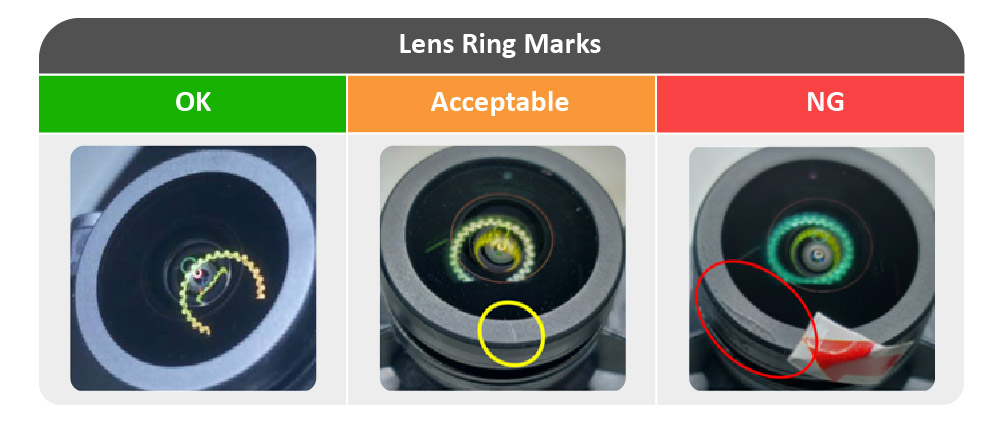
稀なまたは重大な問題の事例紹介
1. タッチパネルのコンソールパネルに白い斑点があり、操作時にユーザーの視覚に影響を及ぼしてしまいます。パネルに白い斑点があると、ユーザーエクスペリエンスが極端に悪くなるため、機能に問題がなくとも重大な問題と見なされることにご注意ください。
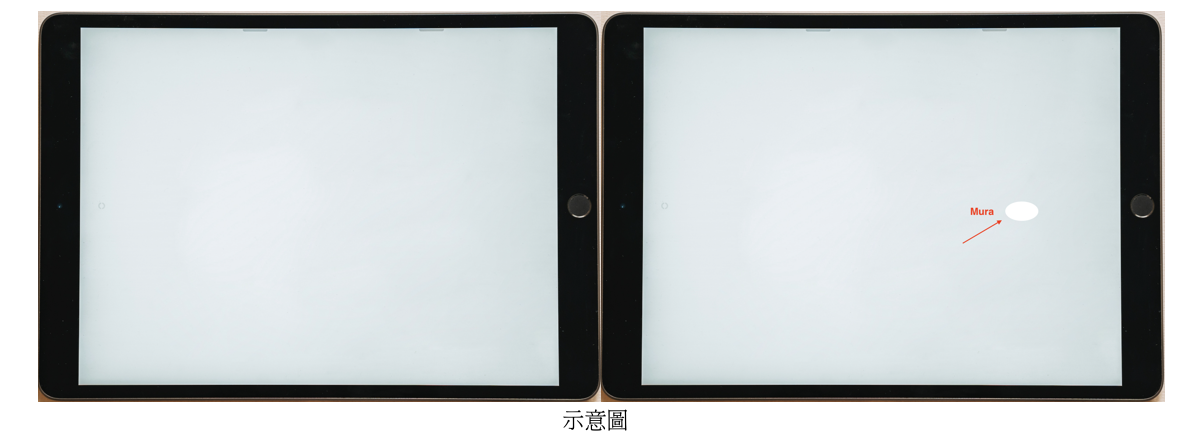
Sampling Rate/ Fail Rate:
当該ロットの520個を100%検査した結果、334個に白い斑点が確認され、発生確率は64.23%にも達しました。
Value:
当社は、製造元が把握していない重大な問題を見つけ出すサポートをしました。当該製品は製造工場での品質管理検査に合格していましたが、アリオンに所属するプロのIQC工場駐在スタッフが検査を行ったところ、やはり異常が見つかり、5個のサンプリングを要求した結果、4個に類似の現象が見られたため、このロットを全数検査に切り替えました。
Root Cause:
①タッチコントローラー背面の底面開口部で、プラスチック樹脂の応力がその周辺に集中し、この部分が変形しました。
②構造設計上、反りが発生しやすく、変形した部分がLCDの背面に当たり、色ムラの原因になります。
③本製品は設計上、開口部とLCDの部分にわずか0.3mmのすき間しかありません。ケースに反りが生じると、場合によってはこのすき間がゼロ以下になり、LCDの背面を圧迫します。そのため、過度の応力が生じ、パネルに圧力がかかることにより変色や色ムラが発生します。
Solution :
アリオンの経験豊富な検証チームは、生産ラインにねじのボスが短い新しいツールホルダーを使用することを提案し、新たに10個を試験生産して検査したところ、すべて異常はなく、新しいツールホルダーで開口部の変形と機構の反りを予防できることを証明しました。この結果をお客様に報告し、承認を得た上でさらに300個を生産し全数検査を行ったところ、問題はありませんでした。
IQCサービスにより、お客様の返品やクレームのコストを削減するだけでなく、製品の信頼性やブランドイメージを大きく向上させることができると言えるでしょう。
2. レンズリングの溝のバリ(破片)付着
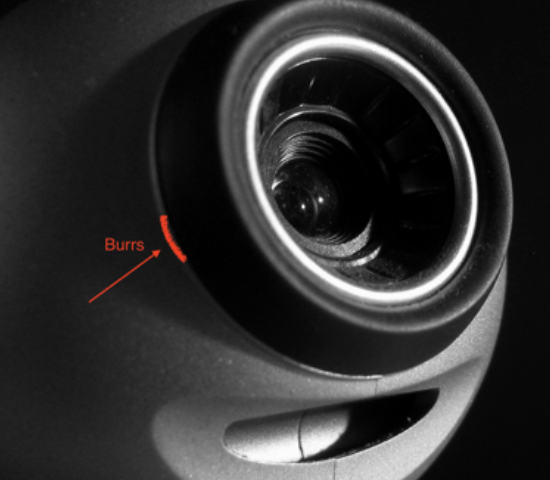
Sampling Rate/ Fail Rate:
100%検査した結果、550個中17個にバリ(破片)が見つかり、問題の発生確率は3%と高い不良率となりました。
Value:
①製造元の既存のOQC(出荷品質検査)のSOPでは、分かりやすい表面の損傷しか検出できず、この問題をとらえることができません。製造元独自の検査SOPを確認したところ、明らかな損傷や機能問題のみに重きを置くあまり、接合部、底部のような細部の外観について検査を行っていないことが判明しました。
②当社は、カメラの外観を損なわずに、製造元が把握していない重大な問題を見つけ出すサポートをしました。カメラは高精度の製品であり、完成品の輸送途中でレンズの前玉が傷つくことで、実際の機能に影響を与えたり、ブランドのマイナスイメージとなったりしないようにするため、不純物や異物の残留は許されません。
Root Cause:
これは、製造プロセスでの見落としに当たります。発注元が製品の外観検査に関する基準や手順を定義していなかったため、製造ラインにも合格品質水準がなく、この部分の検査が行われなかったのです。
Solution:
アリオンは、発注元の承認を得た上で、製造元と協力してサンプルの検査基準を策定し、製品ロットごとに生産ラインの100%のOQCを受けてから出荷することとして、不良品がお客様のもとに渡らないように、返品やクレームによるコスト増加を予防しました。
アリオンIQCサービスの特徴
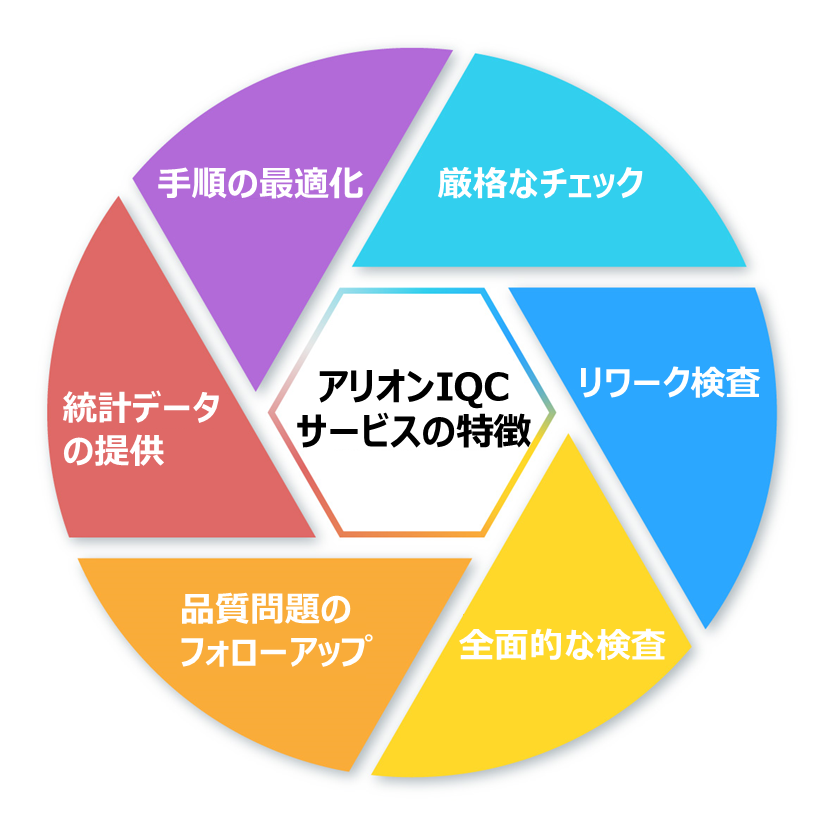
上記の実例はほんの一部となります。アリオンIQCサービスは、生産開始前に潜在的な問題を特定し、最適なソリューションでお客様の検査目標達成をサポートします。当社の品質管理プログラムにご興味をお持ちの方、またはご質問のある方は、お気軽にアリオンのお問い合わせフォームまでお問い合わせください。