SMT(Surface Mount Technology、表面実装技術)とは?
SMT表面実装技術は、電子部品組立業界において最も普及している技術とプロセスです。電子回路表面実装アセンブリ技術(Surface Mount Assembly、略称SMA)は、表面実装または表面アセンブリ技術を意味しています。これはリード端子やリード線の無い表面実装部品(Surface Mount Components、略称SMC/Surface Mount Device、略称SMD)をプリント基板(Printed Circuit Board、略称PCB)の表面やその他の基板の表面に実装し、リフローはんだ付けや浸漬はんだ付けなどの方法で取付ける表面実装技術です。
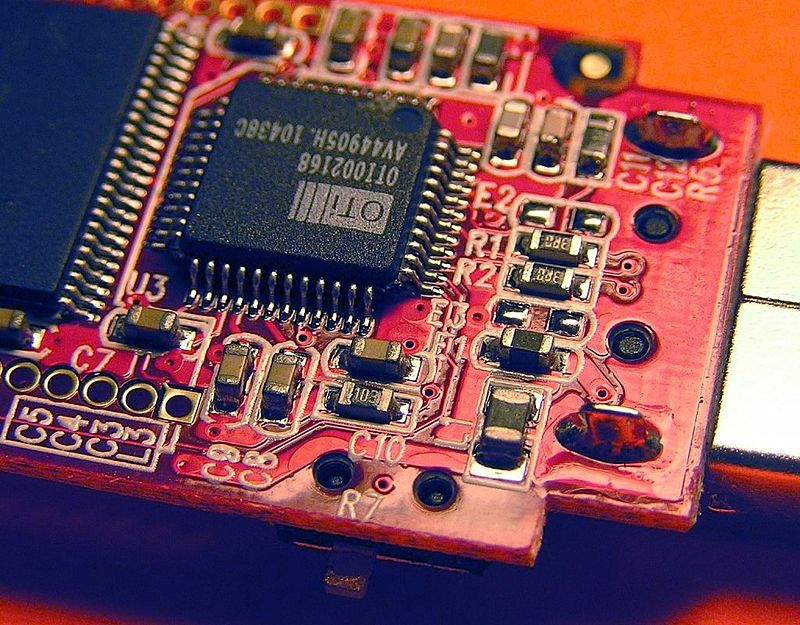
SMTの基本プロセスとは?
SMTは、クリームはんだ印刷工程、接着剤塗布工程、部品実装工程、リフローはんだ付け工程、洗浄工程、SPI工程、検査工程、不良品リワーク工程で構成されています。
部品のはんだ付けのための前準備として、クリームはんだや接着剤をPCB基板のランドやパッドに印刷する工程です。この工程ではクリームはんだ印刷機を使用します。通常SMT生産ラインの最初にある工程です。
部品をPCB基板に仮固定するための接着剤をPCBの固定位置に塗布します。この工程ではディスペンサー(接着剤塗布機)を使用します。通常SMT生産ラインの最初か検査設備の後にあります。
表面実装用の電子部品をPCBの固定位置に配置します。この工程ではチップマウンターを使用します。通常SMT生産ラインのクリームはんだ印刷機の後にあります。
熱ではんだを溶かし、表面実装部品をPCB基板に接合します。この工程ではリフロー炉を使用します。通常SMT生産ラインのチップマウンターの後にあります。
表面実装が完了したPCB基板上の残っている、フラックスなどの人体に有害なはんだ付けの残留物を除去します。この工程では洗浄機を使用します。洗浄設備の設置位置は特に決まっておらず、インラインでもオンラインでも構いません。
Solder Paste Inspectionの略称です。主にクリームはんだ印刷の体積、面積、高さ、位置ズレ、欠損、破損、高さの偏差などの不良検査を行います。
表面実装が完了したPCB基板に対して、はんだ付けの品質と部品実装の品質の検査を行います。この工程では、ルーペ、顕微鏡、インサーキットテスタ(ICT)、フライングプローブ、自動光学検査機(AOI)、X線検査システム、ファンクションテスタ(FCT)などの設備が使用されます。設備の設置個所は、必要に応じて生産ライン上の適当な位置に設置されます。
不良や故障が検出されたPCB基板のリワークを行います。この工程でははんだごてやリワークステーションなどを使用します。設備の設置個所は生産ライン上の任意の箇所です。
部品の配置により基板は2種類に分けられます:
- 片面基板
- 両面基板
- 片面基板の生産フロー
PCB設置 → SN(serial number)などのレーザー印字 → クリームはんだ印刷 → SPI → 部品実装 → AOI → リフロー→ 基板切断 → 検査 → 不良品リワーク
- 両面基板の生産フロー
PCB設置 → SNなどのレーザー印字 → PCBのA面クリームはんだ印刷 → SPI → 部品実装 → AOI → A面リフロー→ 基板裏返し → PCBのB面クリームはんだ印刷 → SPI → 部品実装 → AOI → B面リフロー→ 基板切断 → 検査 → 不良品リワーク
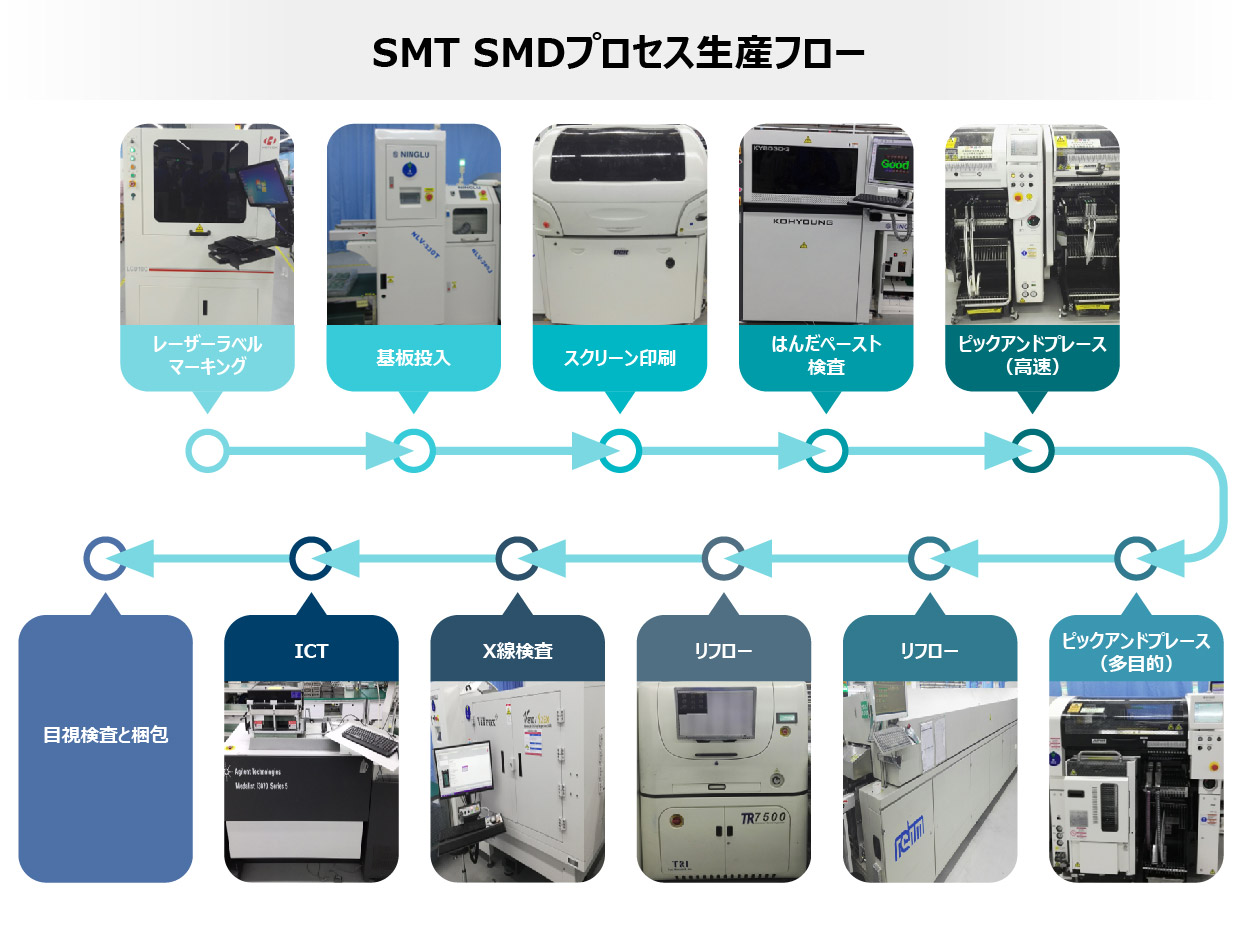
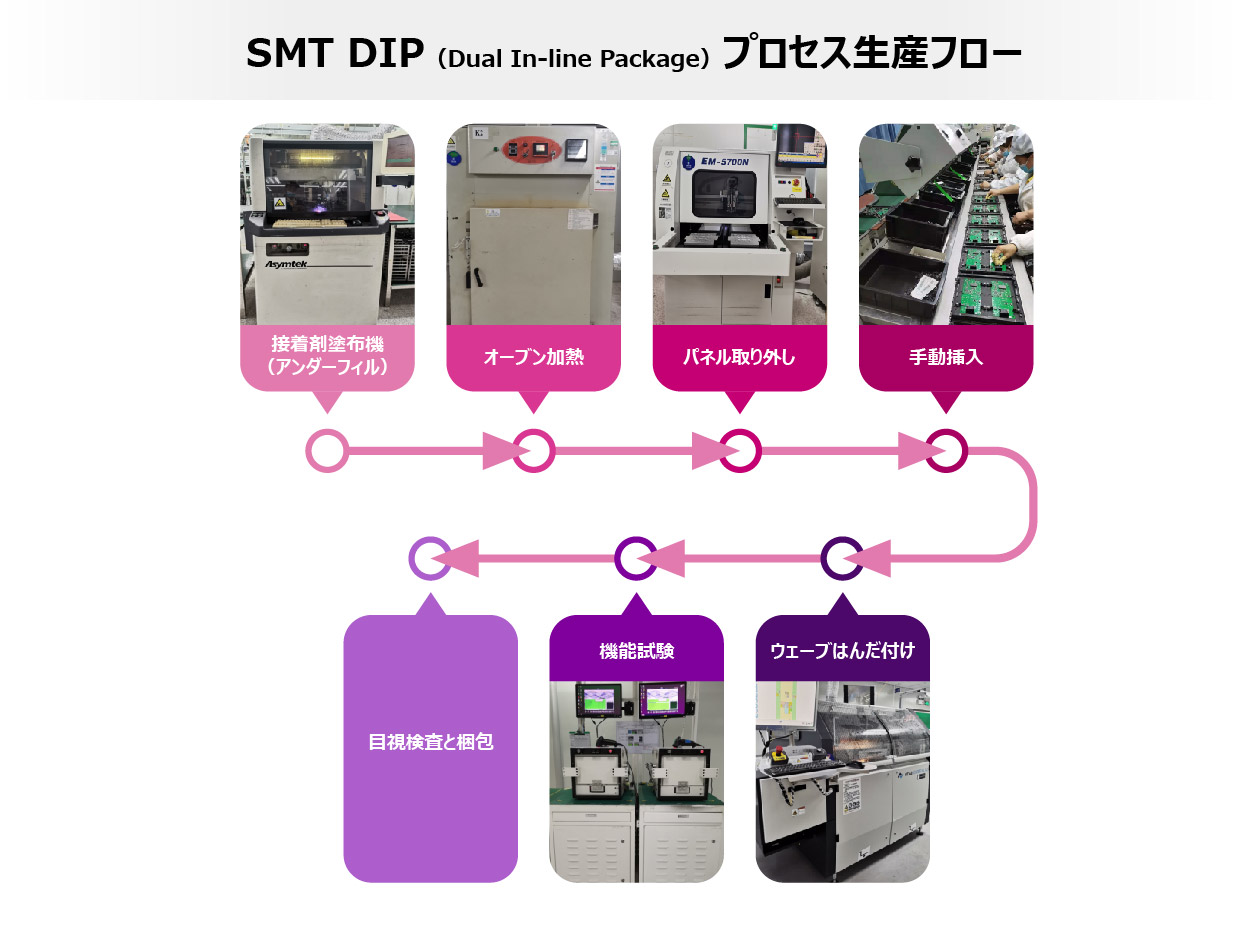
生産ラインで最もよく見られる回路基板の検査はAOIとICT検査の二種類です。この二種類の検査はお互いを補い合う形で使用されています。次は簡単に紹介します:
AOI検査(Automatic Optical Inspection)
自動光学識別システムとして、電子業界の回路基板組み立て製ラインで普及しており、従来の人員による目視検査(Visual Inspection)に取って代わり外観検査を行っています。
AOIの基本原理
画像技術を利用して、検査対象物の画像とリファレンスの標準画像を比較し、その差異で検査対象物が基準を満たしているか判断します。そのため、AOIの良し悪しは、画像の解像度、イメージング能力と画像解析技術で決まります。SMT組立ラインでは、回路基板上のPCBアセンブリ(PCB Assembly)後の品質状態の検査やクリームはんだの印刷状態が基準を満たしているかなどの検査に使用されます。
AOIの一番のメリット
従来のSMTのリフロー前後の人員による目視検査に取って代わり、より精確にSMT部品実装アセンブリの欠陥を判断することができます。
AOIの一番のデメリット
コントラストや陰影、明暗があまりはっきりしていない箇所では、誤判定(false reject)が発生しやすいのが最大のデメリットです。色の違うライトを使用して判断をすることも可能ですが、ほかの部品に遮られている部品や部品の底に位置するはんだ接合部などの検査は困難であり、従来のAOI検査では光が照射された部分しか検出できないので、シールドフレームのリブ構造部やエッジ部の底にある部品は、AOI検査において検査漏れが発生してしまいます。
そのため、プリント基板アセンブリの生産ラインでは、アセンブリの品質検査においてAOI検査のみを使用することはありません。通常はICT(In-Circuit Test)検査およびファンクションテスト(FVT)、更には自動X線検査装置AXI(Automatic X-ray Inspection)を1台追加し、X線を利用して部品の底に位置するはんだ接合部(例えば、BGA)の品質の検査を行い、プリント基板の検査カバレッジを100%にします。
AOI検査ではプリント基板における以下の欠陥を検出することが可能です:
● 未実装、欠品(Missing)
● 位置ズレ-斜め(Skew)
● ツームストーン現象(部品立ち、tombstone)
● 部品違い(wrong component)
● 極性逆(Wrong polarity)
● リード浮き(lead lift)、リード変形(lead defective)
● はんだブリッジ(solder bridge)
● はんだ過少(insufficient solder)
● はんだ不濡れ、コールドジョイント
AOI 欠陥の例:
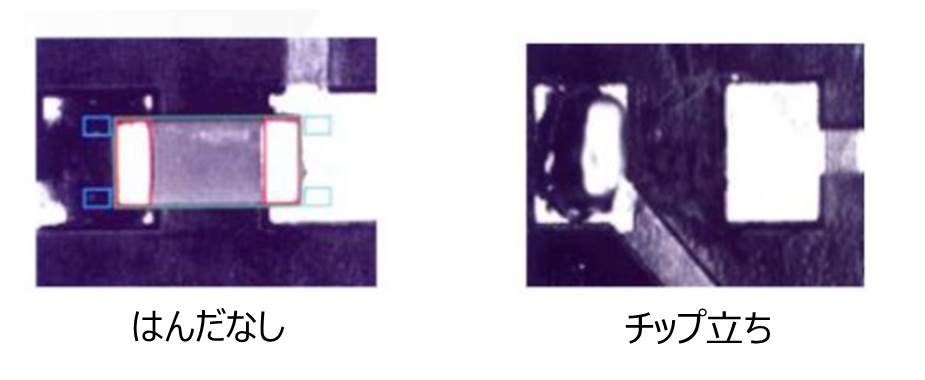
ICT(In-Circuit-Test)
インサーキットテストは「電子回路テスト」または「電気特性テスト」とも呼ばれています。 ICTは主にプリント基板アセンブリ(PCBA、Printed Circuit Board Assembly)の電気特性の検査を行います。電子部品を基板から取り外すことなく、プローブピンを用いて、全ての部品の電気特性およびはんだ付けの状態にショートやオープンなどの問題が無いか検査します。
ICTの動作原理
ピンボードを用いて、プリント回路基板上に予め配置されているテストポイント(Test Point)と接触させて、部品単位またはネット単位のテストを目的としています。
マルチメータで抵抗器を測定する際、プローブを抵抗器の両端に当てるように、ICTでもプローブピンを全ての部品のリード端子から延び出ているテストポイントに当てなければ測定ができません。時には、一列に並ぶ回路や一部の回路を一つの部品と見なし、等価直列抵抗値、コンデンサー値および電圧を測定することもあります。そうすることによってテストポイントの数を減らすことができ、通常そのような測定をネットテストと呼びます。
通常プリント基板のアセンブリにおいて最も多く発生する欠陥は、はんだ付けのオープン、ショート、位置ズレ、欠品、部品違いなどで、全体の不良の約90%を占めています。一部特定の欠陥以外は、ICT検査で不良品を100%検出することができます。なお、部品の「位置ズレ」はICT検査で検出できるとは限りません。なぜなら、部品のリード端子が指定位置にはんだ付けされ導通されていれば、電気特性検査では異常が無く検出されなないからです。実のところこのような欠陥が本当に不良に繋がるかどうかは疑う余地があり、不良とは言い切れない部分もあります。また、コールドジョイントやはんだ不濡れによる接触不良(intermittent)もICT検査では100%検出できません。これはICT検査において最も悩ましい問題であり、ICT検査は電気特性を測定し回路を検出しているため、検査を行う際ちょうど接触不良個所が接触しており、導通がとれていれば異常が検出できません。
ICTテストのメリット
測定時間が短く、速いことです
PCBAに電源を投入して起動しなくてもL/C/R/Dの測定が行えるため、起動にかかる待ち時間を削減でき、ショートによるプリント回路基板の焼損も低減できます。僅か3~5秒間で300個の部品が実装されている回路基板の測定が完了します。
優れた繰返し測定性があります
コンピュータプログラムによる制御と高度な測定精度で誤判定と測定漏れのリスクを大幅に低減し、生産ラインにおける問題を低減することができます。(テストポイントの接触不良による誤判定の可能性はある)
現場技術の依存性が低いことです
ほぼ全てコンピュータ制御なので、人為的な操作時間と操作ミスを大幅に低減することができます。通常のオペレータでも、少し訓練をすれば簡単に設備の操作や検査治具の交換を行うことができます。(テストプログラムは専門の技術者やエンジニアによるメンテナンスが必要)
製品修理のコストを大幅に削減することです
通常のオペレータでも製品の修理作業が行えるため、人員コスト削減に効果的です。ICT検査ではコンピュータプログラムを通じて、どの部品またはどのネットに問題があるかを伝えてくれるので、技術者による不良の再測定とデバックの効率を大幅に向上させることができます。
生産スループット(throughput)を向上させることです
迅速な測定とフロントエンドのSMT作業に対してリアルタイムに問題をフィードバックすることにより、生産の不良率を低減し、部品の在庫および不良品の在庫を減らすことができ、コストを削減できるため、競争率と製品の品質向上に繋がります。テストポイントが足りていれば、バイパス(by pass)回路上の部品を含め、プリント基板上の全ての回路と部品の測定をICT検査でカバーできるため、製品の品質を向上させ、顧客クレームを低減し、最終的には業績アップに繋がります。
ICTテストのデメリット
通常ICT検査用の設備と治具の費用は高価であり、特にエアプレス式のスチール材治具は、200万円~250万円かかることもあり、比較的大量生産向けの製品検査に適しています。
ICTテストを使用する場合、ピンボードと接続させるために、プリント基板上にテストポイント(Test Point)を設ける必要があり、プリント基板のレイアウトの使用率を下げてしまいます。
テストポイントは表面処理の違いによって、異なる接触不良問題が発生します。例えば、OSPの基板はテストポイントの導通を取るためにクリームはんだを追加で印刷しなければなりませんが、クリームはんだ上にフラックスがあると、保護膜が成形されてしまい、接触不良に繋がります。
ピンボードとプローブの正常な動作を維持し、基板の部品に対して電子式ファンクションテストを行うため、ピンボードとプローブは定期的に交換する必要があります。
[/accordion-item] [/accordion]AOIはICTではプローブ測定できない基板に対して光学検査を行えます。
生産ラインでICTとAOIをうまく組み合わせると、生産効率と品質の信頼性を強化することが可能となります。
Allion SMT QCが提供しているサービス(IPQC/OQC)について
アリオンはSMTに対して、以下四つのサービスを提供しています。
1. 新規サプライヤー資格の審査
システム審査と生産工程審査の二種類に分けられています。
システム審査では:システム、環境、安全衛生管理、材料受け入れ品質管理、生産プロセス品質管理、出荷品質管理、品質ツール、クレーム、トレーニング、装置管理、ドキュメント管理に対して審査を行います。
生産工程審査では:クリームはんだ管理、メタルマスク管理、ESD管理、リワーク管理、SFCS管理、SMT生産管理、倉庫管理に対して審査を行います。
生産ラインで最もよく見られる回路基板の検査はAOIとICT検査の二種類です。この二種類の検査はお互いを補い合う形で使用されています。次は簡単に紹介します:
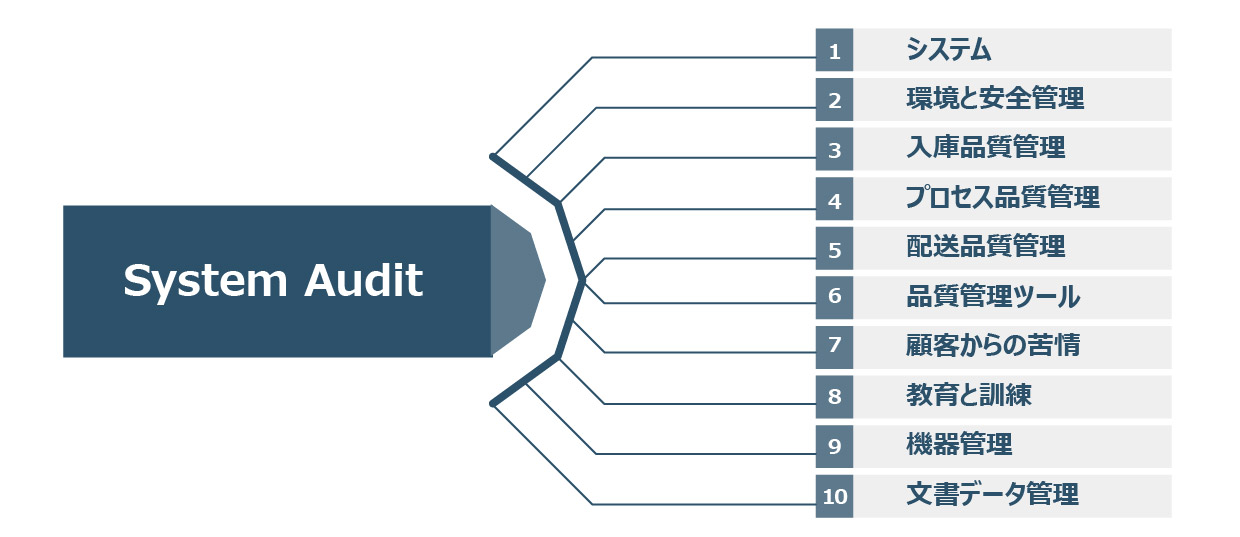
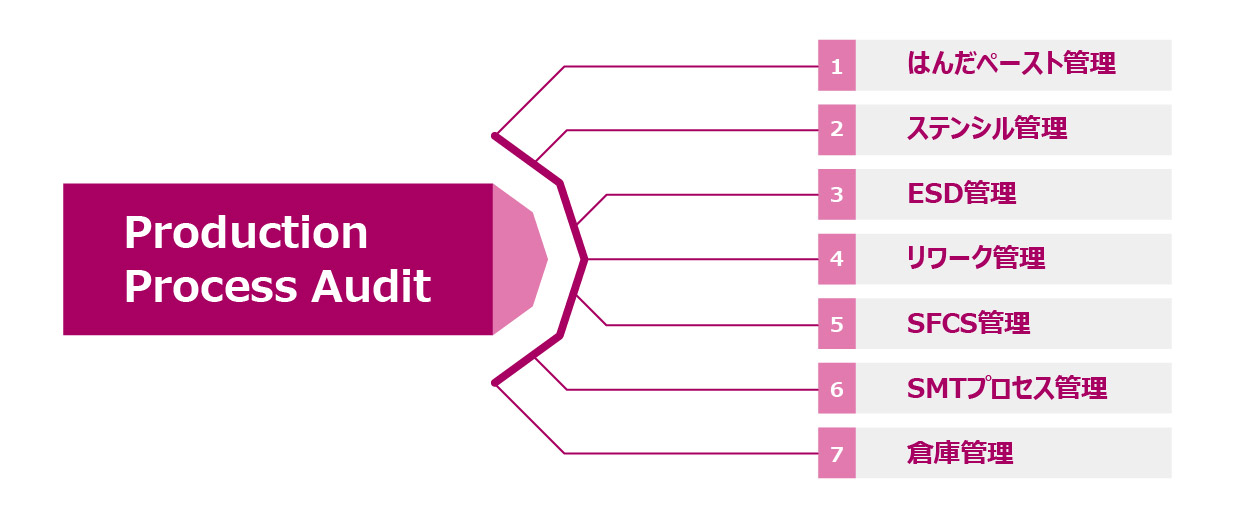
2. SMT IPQC監査・点検表
各生産プロセスの品質を厳しくチェックします。
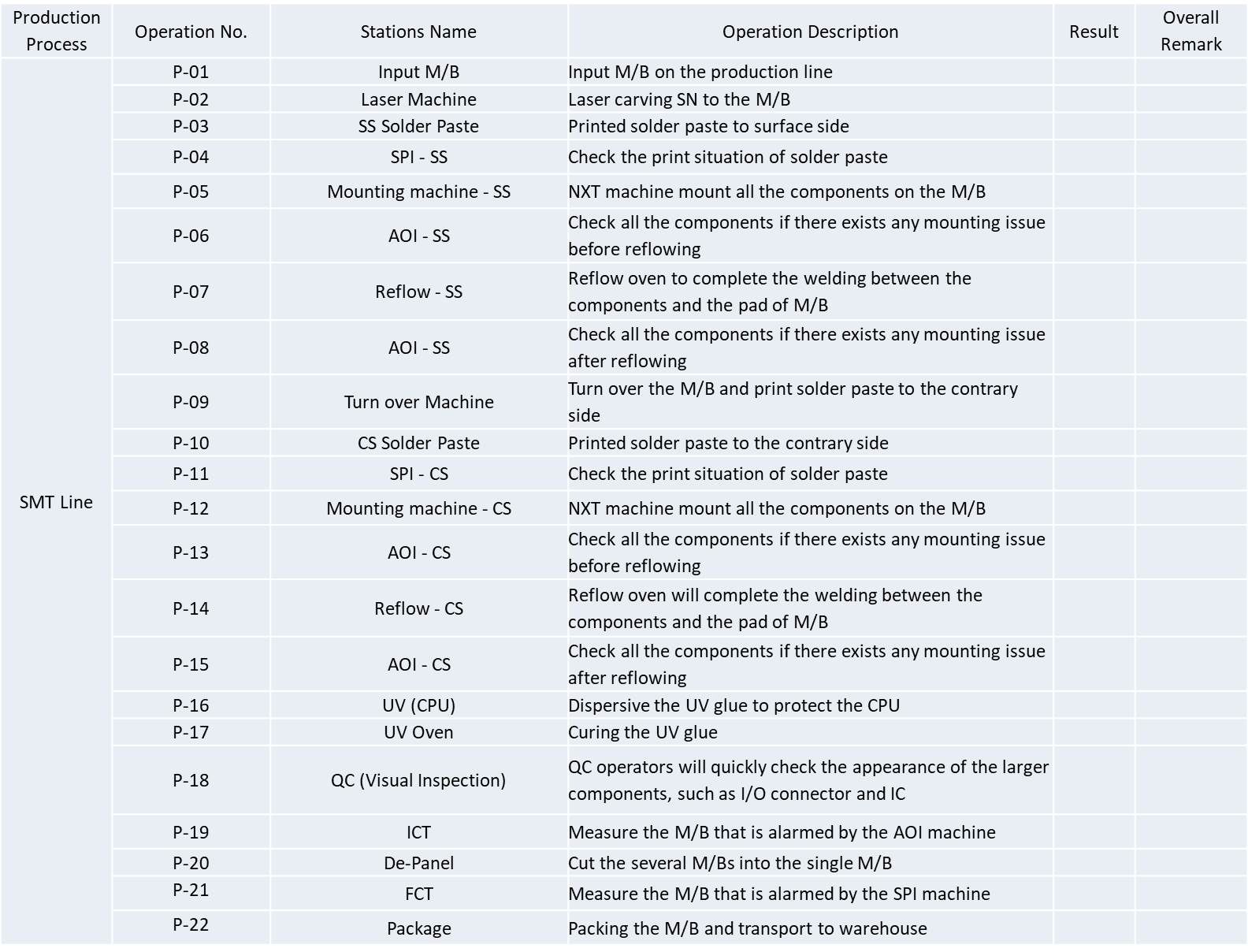
3. SMT歩留まり向上
各生産プロセスの品質を厳しくチェックします。
・SMT現場監査を行います。
・OQC検査をします。
・毎週サプライヤーとミーティングを行い、当週のSMT品質報告を審査します。
・サプライヤーと問題点の分析を行い、改善を実施します。
4. SMTによくある問題点の分析
はんだ不良、位置ズレ、欠品、ツームストーン現象、浮きなどの問題点を発見し、原因を分析します。
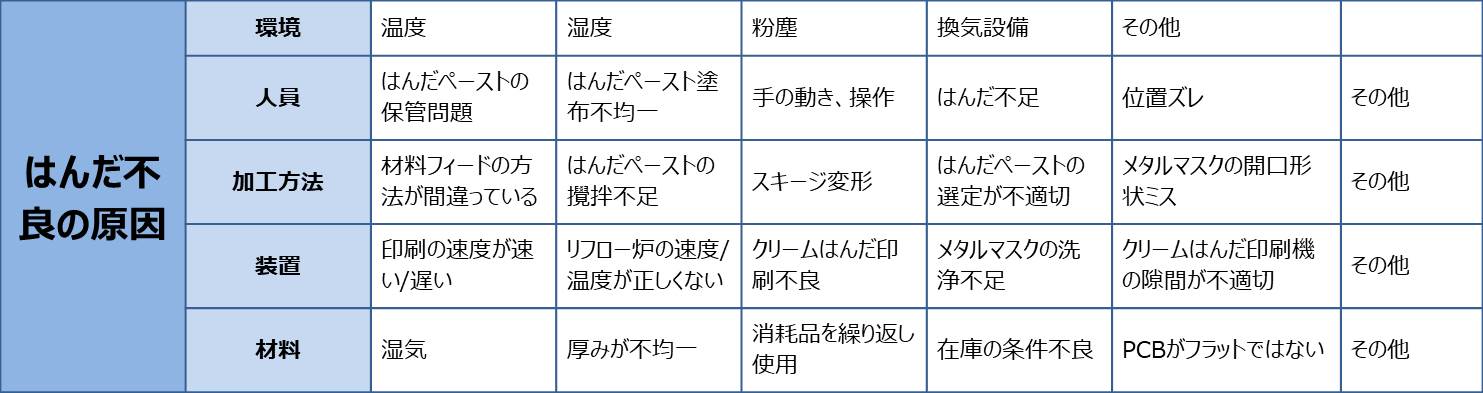
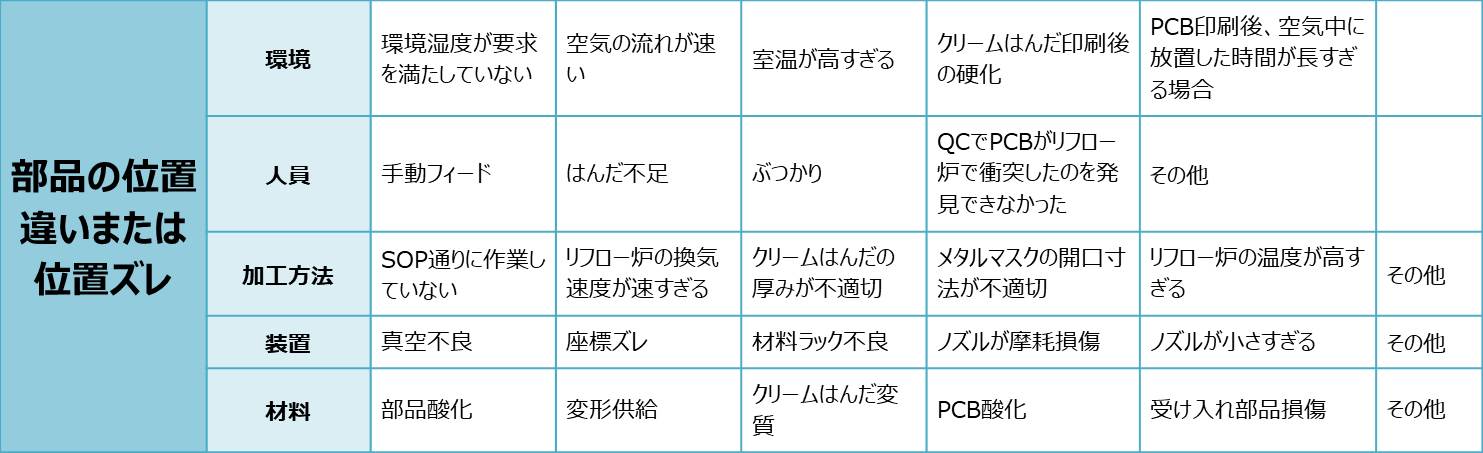
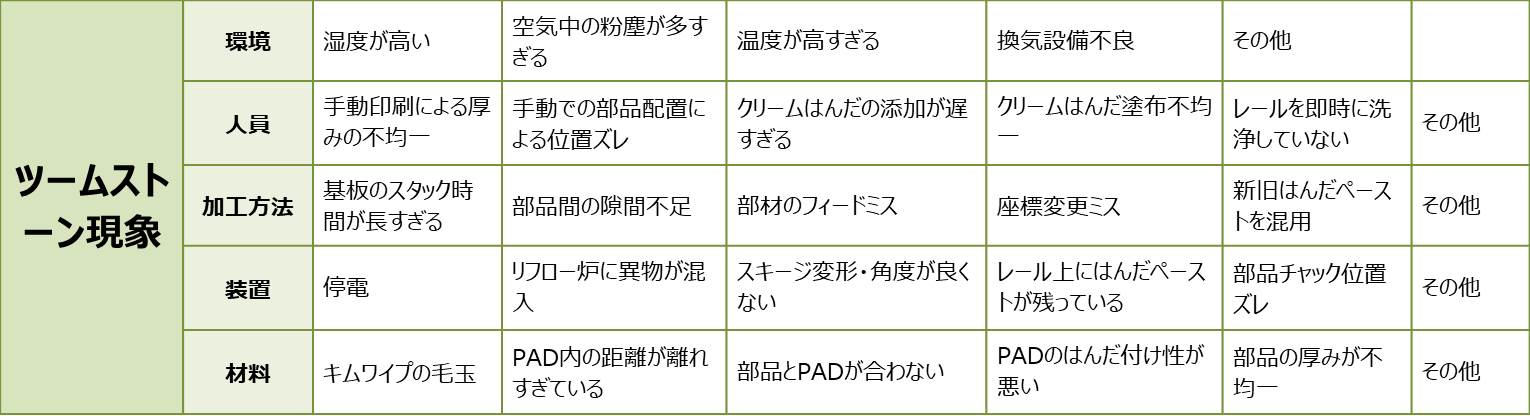
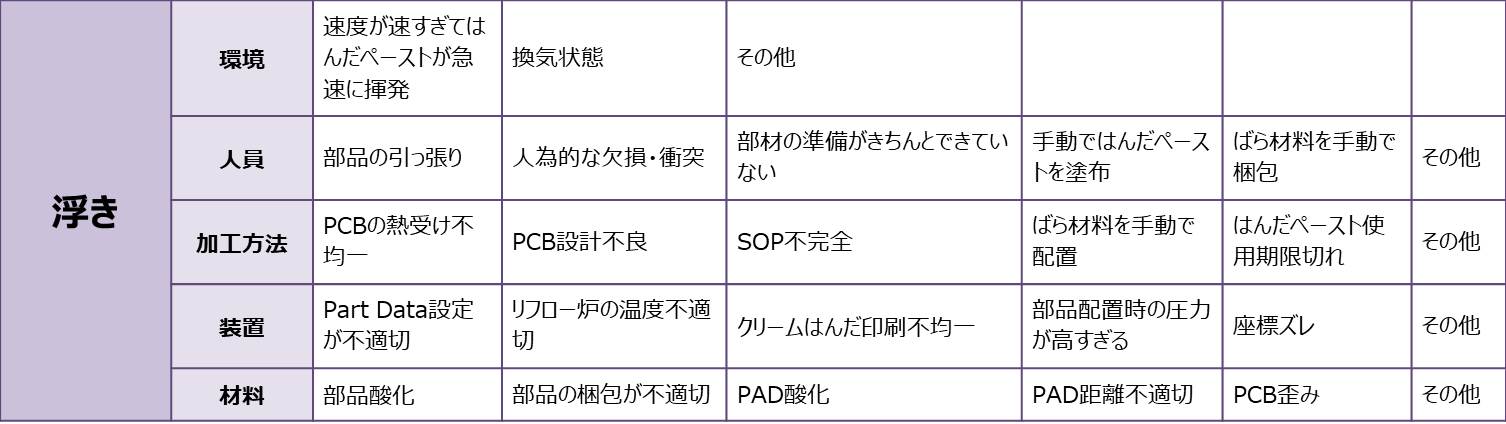
サービスの特長
データと数値を用いて問題点を解決
工場で突発異常が発生した場合、科学的な作業方法とプロセスに基づいて、一歩一歩問題を深く分析し、解決します。作業の過程においてデータと数値を用いて事実に基づいた説明と科学的な方法での問題解決にこだわりを持っています。品質の改善、コストの低減、経済的効果の向上を理念とし、アリオンは専門能力と素質をより高め続け、積極性と創造性を呼び起こします。
品質管理活動の実績があり
ODM工場の品質審査から、製品開発能力、受注状況、材料購入、受け入れ検査、生産プロセス管理および出荷管理、アフターサービスまで、アリオンはODMと仕入先・委託先間の掛け橋として、それぞれの段階でお客様のニーズを応じた品質管理活動に貢献しています。
SMT向けの品質管理体制
SMT全工程の品質管理は一つのシステムの工程とされており、安定した生産品質を得るため、アリオンでは設計、材料、現場のプロセスなどに対しシステムを通じて管理を行います。プロセスの要求を確実に実現することを管理目的としており、全ての過程において品質の安定性を維持するため、SMTのプロセス要点(プロセス方法と要求、技術のキーポイント)や工程知識を把握するほか、よくあるはんだ付け不良に対し対策を行い、効果的な品質管理体制を整え、生産プロセスにおける問題点を迅速に解決します。
次の記事では、現場の第一線で起こっている問題点の分析について紹介する予定ですので、ぜひ乞うご期待ください。
アリオン生産管理・品質向上支援サービスについて、ご興味のある方はお気軽にお問い合わせフォームよりご連絡ください。